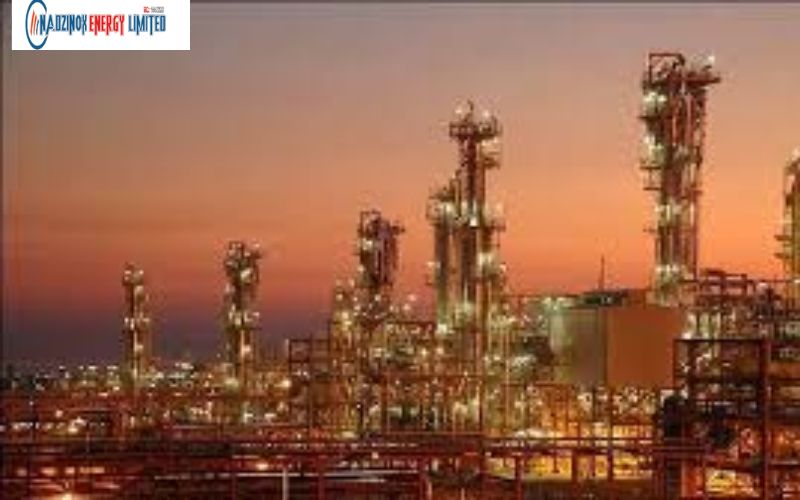
Processing & Refining Equipment: Transforming Crude Oil into Usable Products
Crude oil, as extracted from the wellbore, is a complex mixture of hydrocarbons with limited direct applications. Processing and refining equipment play a vital role in transforming this raw material into a vast array of usable products, from transportation fuels like gasoline and diesel to petrochemicals used in everyday items. Here's a closer look at the key categories:
1. Distillation Towers & Separators:
Distillation Towers (Fractionation Towers): These are towering vertical vessels that utilize the principle of fractional distillation to separate crude oil into its various hydrocarbon components based on their boiling points. Lighter components like gasoline and naphtha rise to the top,
while heavier fractions like diesel and fuel oil collect at lower levels.
Gas Separators: These vessels separate natural gas streams from the liquid hydrocarbon stream coming from the distillation tower. They may also be used to separate different gas components,
such as removing water vapor or condensate from the natural gas stream.
2. Reactors:
Reactors are vessels where chemical reactions are induced to further process and convert the various hydrocarbon fractions obtained from the distillation towers.
Here are some examples:
Hydrocrackers: These reactors use hydrogen under high pressure and temperature to crack heavier hydrocarbon molecules into lighter,
more valuable products like gasoline and diesel.
Fluid Catalytic Crackers (FCCs): FCCs utilize a hot catalyst bed to crack heavier fractions into gasoline, LPG (liquefied petroleum gas),
and olefins, which are building blocks for various petrochemicals.
Alkylation Reactors: These reactors combine lighter olefins to create high-octane gasoline components, improving the quality and anti-knock
properties of gasoline.
3. Storage Tanks & Terminals:
Similar to the ones used in the transportation and storage sector, storage tanks play a crucial role within refineries. These tanks hold various intermediate and finished products during processing and before transportation to distribution centers.
Here are some additional considerations:
Loading Arms & Valves: These specialized loading arms and valves facilitate the safe and efficient transfer of refined products from storage tanks to trucks,
pipelines, or barges for transportation.
Blending & Mixing Equipment: Refineries often blend various refined products to achieve specific properties for different applications. Blending equipment allows for precise mixing of gasoline components, diesel grades,
or other products based on desired specifications..
4. Instrumentation & Control Systems:
Modern refineries rely heavily on sophisticated instrumentation and control systems to ensure efficient and safe operation. Here are some key components:
Process Control Systems (DCS): These are computerized systems that monitor and regulate various parameters within the refinery, such as temperature, pressure, flow rates, and levels.
They allow for real-time control of the entire processing chain.
Analyzers: Various analyzers are used to monitor the composition of feedstocks, intermediate products, and final products. These include gas chromatographs for detailed hydrocarbon analysis and mass spectrometers for identifying specific components within the
refinery streams.
Safety Instrumented Systems (SIS): These are critical safety systems that automatically shut down operations in case of emergencies like equipment failure, pressure surges, or fire.
They play a vital role in ensuring plant safety and protecting personnel and the environment.
By utilizing this complex array of processing and refining equipment, oil and gas companies transform crude oil into a vast range of valuable products that fuel our daily lives and form the building blocks for countless industrial applications.